What is Bubble deck Slab?
The slab that comprises of plastic void balls in middle which are sandwiched between top and bottom mesh to reduce the dead weight act on the slab
It is a biaxial hollow core slab where the concrete which is not performing any structural function are eliminated lead to reduction in 30% to 50% of its slab weight
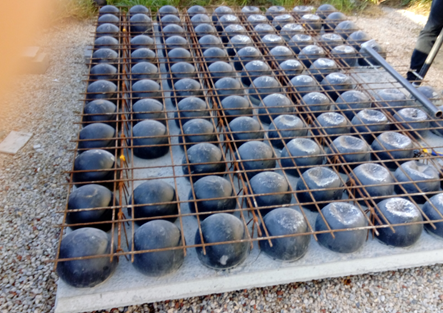
Principle:
The Hollow plastic balls clamped with the top and bottom reinforcement are placed in the thin concrete of 60mm with max length and width of 10m x 3m to form a precast setup will be done in factory. After that the setup will be installed on site with connecting rods and by pouring concrete
The 35% saving in concrete composition was achieved by the ratio of Plastic ball diameter to the thickness of the slab depth
The reduction in slab weight leads to achieve the Load bearing capacity at a smaller slab thickness result in saving 40 to 50% of material consumption per Floor level.
Materials for Bubble deck slab:
Concrete
- Standard with max aggregate size of 20mm
- No plasticizers needed for concrete mix
- Grade of concrete must be above M30
Reinforcement
- Grade Fe-600 strength or high
- Top mesh and Bottom Mesh reo of N12 bars max
- Truss arrangements for vertical support of balls. Truss height depends on slab depth
Plastic Balls
- Hollow sphere Plastic balls made of Polyethylene
- Diameter of balls are depends on the Slab Depth. Ball sizes are 180mm, 225mm, 270mm, 315mm and 360mm.
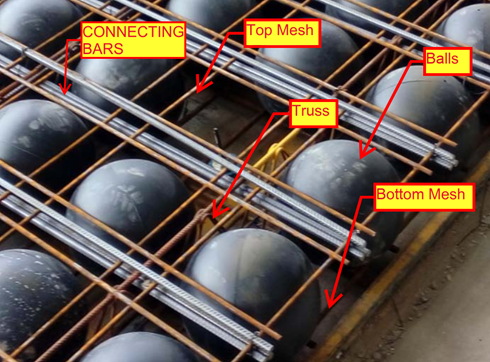
Applications of Bubble deck Slab
Superior Architectural Design
- Free choice of shape
- Large corbels
- Large spans and cantilever
- No beam and fewer column results in flexibility
- Interior design can be easily being altered.
Advantages:
Structural
- Reduce the foundation size since 50% of the dead weight is already reduced by the slab.
- Increased Strength due to biaxial Loading.
- Longer spans are supported since no bean is required.
- Column count can be reduced.
- Excavation required less work.
- Conduits and openings for service ducts can be easily incorporate in factory.
Construction
- Less equipment is required due to light in weight.
- Less work on Site construction.
- Shuttering work and its Dismantling is not required since the 60mm concrete biscuit will act as shutter.
- Construction hours and time taken is very less compare to conventional Slab
Engineering
- High resistance against explosion due to biaxial flat slab system.
- High Resistance to earthquake due to slab acts as elastic vertical structure.
- User friendly to Post tensioning if running through slab.
Environment
- CO2 emission due to concrete manufacturing quantity are reduced
- Less material consumption
- Less energy consumption
- Less wood as no horizontal scaffolding
Economy
- Sustainable for easy installation
- Made to measure and saving material
- Fast Implementation and construction
- Reduction in Transportation Loading cost.
- No shuttering and its cost needed
Disadvantage
- Deflection will less higher than the Conventional Slab
- Load carrying Capacity is lesser than the Conventional slab
- Skilled labour required
- Shear Load design consideration and its factor near the column area to slab care is required
Thanks for this very relevant topic for bubble deck slab. Very informative… Because Bubble deck slab has a superiority over the conventional slab as it has reduced weight, increased strength, fewer columns and no beams or ribs